Why waterjet cutting is simply the best for aerospace applications
When it comes to cutting aerospace materials, precision is critical. And, simply because of the natural pressures of business, manufacturing speed doesn’t lag far behind in importance.
This is why waterjet cutting is an unmatchable solution for aerospace production.
Waterjet cutting is ideal for precision cutting
Simply put, waterjet cutting on metal is incredibly accurate — able to deliver pinpoint cuts within tolerances of as little as 0.001 of an inch.
What’s more, they deliver this self-same precision even when working with large and oversize components. In fact, waterjet cutting can easily handle blocks of aerospace metals that are as much as 18 inches thick.
Waterjet technology also reigns supreme for its precision when cutting complex shapes and designs. This is especially useful in aerospace for delicate componentry such as gears.
Waterjet cutting mean no Heat-Affected Zone (HAZ)
Additionally, because of its nature, waterjet cutting does not produce what’s called a “heat-affected zone” (HAZ) on the material.
Other cutting methods — such as laser- or plasma-cutting — generate heat in the part. This can cause structural changes that warp or distort materials that are sensitive to excessive temperatures. The nature of waterjet cutting preserves temperature-sensitive materials' structural integrity, eliminates any potential warping and ensures high-quality results necessary for aerospace projects.
Waterjet cutting is simply faster
Waterjet cutting also doesn’t require tool changes, or someone to set up new cutting parameters for different materials or thicknesses, or even for the machinery to warm-up before operation. As a result, waterjet cutting can cut through a wide range of materials quickly and efficiently, without the need for tool changes or heating up the material.
Since the cutting process don’t generate heat, also there’s no need to wait for the material to cool between cuts. Plus, waterjet cutters can be configured to cut in multiple axes — they can cut complex shapes and contours in a single operation. This can reduce the number of setups and operations required.
All these things can increase cutting speed, save time and improve overall manufacturing throughput.
Waterjet cutting is incredibly versatile
Waterjets are also able to efficiently cut all sorts of metals, including aluminum, stainless steel, copper, brass, and even more exotic metals like titanium and Inconel. The versatility of cutting materials makes waterjet cutting an excellent for the demanding requirements of aerospace manufacturing.
The adaptability of waterjets is also another reason they are valuable tools, especially when cutting intricate or small designs. Aerospace waterjet cutting metal applications includes precision-cuts of thin, thick, rigid, or soft metal — and even materials such as foam, rubber, fabric, glass and plastics.
Waterjet cutting reduces material waste
Waterjet cutting produce extremely fine cuts using a narrow stream of water. This, in itself, reduces material waste and improves cost-efficiency and sustainability. Furthermore, it is a more responsible choice because waterjet cutting does not produce harmful fumes, gases, or waste products.
The IRWaterjet technology advantage
IRWaterjet's advanced waterjet technology gives those working with aerospace products the advantage of precision cutting, versatility, and sustainability. We are committed to delivering high-quality waterjet components so you can complete all your metal-cutting projects efficiently and effectively.
IRWaterjet's high-pressure, premium-quality replacement components support waterjet equipment, allowing customers to cut a wide range of metals used in the aerospace sector.
Leave a comment
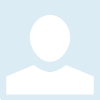